-
Notifications
You must be signed in to change notification settings - Fork 3
Dendrometer
Recommended Due Date for 2026 Growing Season orders: February 14 2026
Changes are actively being made, check updates for current progress
Project Lead: Nicholas Le (Electrical) - leni@oregonstate.edu
Project Members: Lars Rasmussen (Mechanical) - rasmusla@oregonstate.edu
As agricultural demand for freshwater escalates amid climate change, optimizing irrigation management is paramount for resource efficiency and sustainability. Soil water deficits adversely affect crop yield and quality by impeding plant growth and development. Dendrometers, which measure stem diameter fluctuations, offer potential improvements in irrigation management for high-value woody perennial crops by correlating these fluctuations with traditional water stress metrics. However, traditional methods face precision challenges due to mechanical hysteresis and thermal expansion.
The OPEnS Lab addresses these issues with a high-precision dendrometer utilizing zero-thermal expansion carbon fiber, a frictionless spring tensioning approach, and a linear magnetic encoder, achieving up to 0.5-micron resolution. Thermal fluctuations are minimized to less than 1 micron over diurnal swings of 25°C. Depending on the build quantity, the device costs between $250 and $600 per unit, with assembly taking 4 to 6 hours. The dendrometers, equipped with LoRa and WiFi telemetry under evaluation, can operate for over two years on battery power without solar charging. Mass deployment promises a continuous record of water stress-induced stem dimension changes, enhancing decision support for irrigation management.
In the 2024 growing season, these dendrometers are being tested on various crops, including blueberries at Lewis-Brown Farm, hazelnut trees at the North Willamette Research and Extension Center, and cacao trees at Biosphere 2. New designs used in 2024 informed by ongoing research accommodate larger plant stem sizes with larger wishbones and stability by using 3 springs between the wishbone and frame. This innovative approach integrates advanced field sensing, data management, and decision-support systems, contributing to the sustainability transitions of the agricultural sector.
Specification | Sensor | Accuracy Range | Full Range | ||
---|---|---|---|---|---|
Value | Metric | Value | Metric | ||
Senses Linear Motion | AS5311 | 0.5 | µm | 0-1.5 | cm |
Senses Ambient Temperature | SHT30 | 0.3 | ℃ | -40-125 | ℃ |
Senses Humidity | SHT30 | 3 | % | 20-80 | %RH |
Senses Soil Moisture (Optional) | TEROS10 | 0.03 | m3/m3 | 0.00-0.64 | m3/m3 VWC |
Data Collection Frequency | 1 | Seconds | 15 | Minutes | |
Wishbone Size | 45-65 | mm | |||
Larger Wishbone Size | 70-135 | mm | |||
Battery life LoRa (6600mAh) | 4 | Months | |||
Battery life LoRa (10050mAh) | 6 | Months | |||
Low Cost | <300 | $ | |||
Logs Data to SD | Time | date/hour/min | |||
SD and USB are easily accessible | |||||
Removable for winter time | |||||
Data transmits using telemetry | LoRa or Wi-Fi |
Understanding the water stress that crops are experiencing provides valuable information regarding plant development and gives feedback that can assist in more effective irrigation schedules. Water scarcity in regions common for fruit production, coupled with an increasing world population makes the use of precise irrigation techniques in orchards unavoidable [2]. Past research indicates a tendency to over-irrigate early in the season, when water supplies are plentiful, leading to enhanced drought in later months and sacrificing overall crop health. Continuous measurements of plant water stress can conserve water, leading to healthier crops and sustaining essential ecosystems. This increased robustness can have long-lasting effects on the overall well-being of agricultural areas.
Figure 1: Shows general pattern of diurnal fluctuations in plant stems. Expected Maximum Daily Shrinkage (MDS) in grapevines is around 200um.
Many alternate dendrometer devices lack precision and accuracy due to the limitations of the technology employed. In particular, band and point Dendrometers encounter a significant amount of friction which leads to difficulty in achieving highly accurate data measurements. Furthermore, delays or “stickiness” between parts leads to issues with hysteresis: as a plant’s stem switches between expanding and contracting throughout the day, the instrument is unable to measure and record these micrometer motions. A potentiometer restricts the form factor of the mechanical design and exhibits temperature dependency, sacrificing the ability to achieve high-resolution measurements. Additionally, material expansion of the physical components of a Dendrometer leads to inaccuracies in the data recorded by presently available Dendrometers. As outdoor air temperature fluctuates, the material that the Dendrometer is made of will experience expansion/contraction as well, skewing the data so that it reflects this movement instead of the plant’s growth.
The Dendrometer produced at the OPEnS lab seeks to mitigate these effects. By utilizing a frictionless set-up, the impacts of hysteresis are minimized and small fluctuations in both diameter expansion and contraction are measurable. The use of a magnetic encoder as opposed to a potentiometer enables high-precision measurements to 0.5μm. Moreover, the OPEnS Dendrometer employs the use of carbon fiber: a material known for its extremely low coefficient of thermal expansion. This ensures that material expansion/contraction does not confound with plant stem diameter measurements. A more accurate, precise, and accessible Dendrometer can help advance agricultural techniques and plant care methods so they are more responsive to a crop’s immediate needs and small-scale issues can be pinpointed to particular plots within a crop. The refinement of such methods is crucial for advancing agriculture towards a more sustainable future.
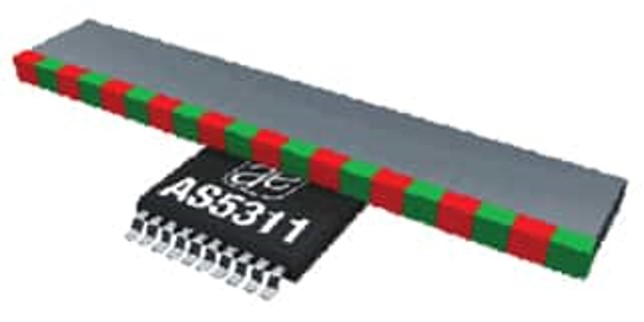
The electronics are comprised of a microcontroller, a Hypnos board, a PCB, and the sensors. The microcontroller that is being used is the Adafruit Feather M0 LoRa. The code is uploaded to the Feather and it communicates with the rest of the hardware. The Hypnos board is the component that manages the system's power, timestamps the data measurements, as well as contains the microSD card that the data is stored to. The onboard real-time clock (RTC) keeps track of the time and turns on the system every 15 minutes. In addition to the 15 minutes, an interrupt button is also installed that allows the user to wake the system up at any time to check the status of the magnet and whether it's in a good position (usually when the magnet is parallel and within 0.2-0.4mm of the sensor). The PCB is custom made that allows the Feather and Hypnos to easily connect to the remaining sensors.
The sensors being used are the SHT30 (to measure temperature / humidity), a Neopixel LED (to indicate to the user whether the magnet is in a good position or not), and a AS5311 magnetic encoder (to measure the stem fluctuation throughout the day). Optionally, a TEROS10 may also be connected to monitor soil moisture at the same time. Every time the system turns on, the sensors take a measurement and records the values to the SD card. Through the Feather, the data is also transmitted at set intervals through LoRa communication to a hub that publishes the data to an online MongoDB database to monitor the system status remotely. Afterwards, the system shuts off to conserve battery life.
The methods to construct the mechanical body have been optimized using a waterjet cutter.
As aforementioned, one key aspect of the OPEnS Dendrometer is the usage of a carbon fiber frame. Carbon fiber is lightweight and has a coefficient of thermal expansion approximately equal to zero [Engineering Toolbox]. The use of carbon fiber ensures that stem diameter measurements are not overshadowed by material expansion within the device. As a tool intended for use in the field, where temperatures can be highly variable, this is an important feature for achieving precise and accurate measurements.
Another essential advantage of the OPEnS Dendrometer is the frictionless mechanics. By relying on a spring-loaded design, all movement recorded by the magnetic sensor is guided by tension; there is no opposition caused by friction that could impede upon measurement accuracy.
The Slider on the dendrometer is removable and can be adjusted for use on stems 25-50mm in diameter. This part of the dendrometer is held against the vine by tension from the spring; as the stem expands and contracts throughout the day, the spring allows the Slider to move with the vine growth. This creates linear motion for the Wishbone, while the Frame remains stationary against the vine. Hence, the magnet, which lies on the underside of the Wishbone, moves back and forth while the AS5311 sensor is held in place by the Frame. The linear movement of the magnet relative to the sensor enables micrometer diurnal fluctuations in stem diameter to be tracked.
Show More
Figure 1: Plot of Dendrometer displacement (orange) and VPD (blue) of a cacao tree located at Biosphere 2 from July 12 to July 31 2024. Packets represent measurements taken every 15 minutes.
Figure 2: Dendrometer deployed on a cacao tree at Biosphere 2
Show More
Figure 1: Data from a dendrometer that was deployed at OSU’s Southern Oregon Research Extension. The data was taken from a grapevine at DANCIN Vineyards, over the course of the 2023 growing season from June to October.
Show More
Seventeen dendrometers were installed on grapevine trunks (Vitis vinifera L.) at Southern Oregon Research and Extension Center (SOREC) in Central Point, OR during the summer 2021 growing season. The devices were deployed for 6-12 weeks on plots receiving two different water treatments.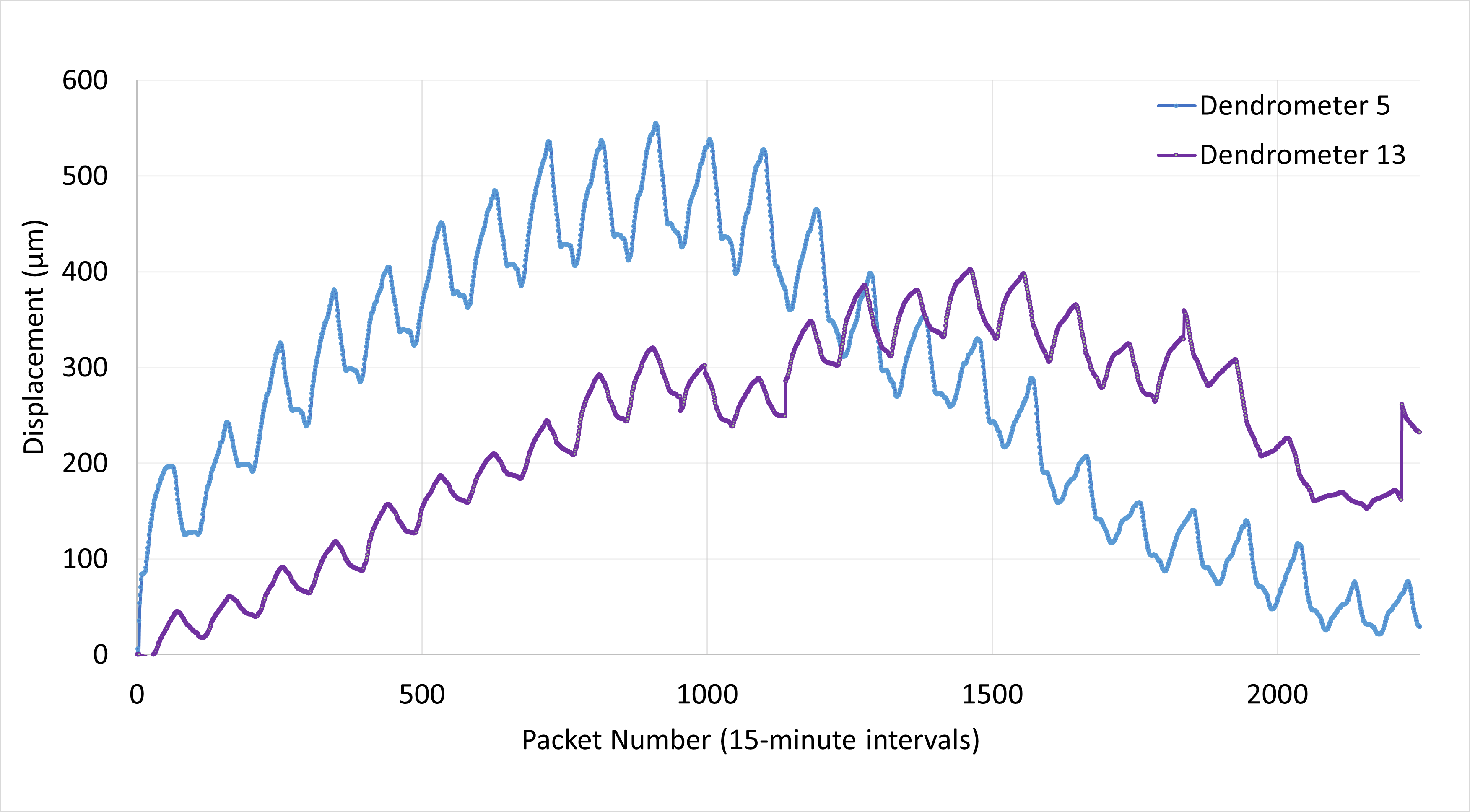
Figure 1: Displacement data from two dendrometers at SOREC for one month of the summer deployment. Dendrometers 5 (blue) and 13 (green) received different irrigation treatments for the duration of the growing season.
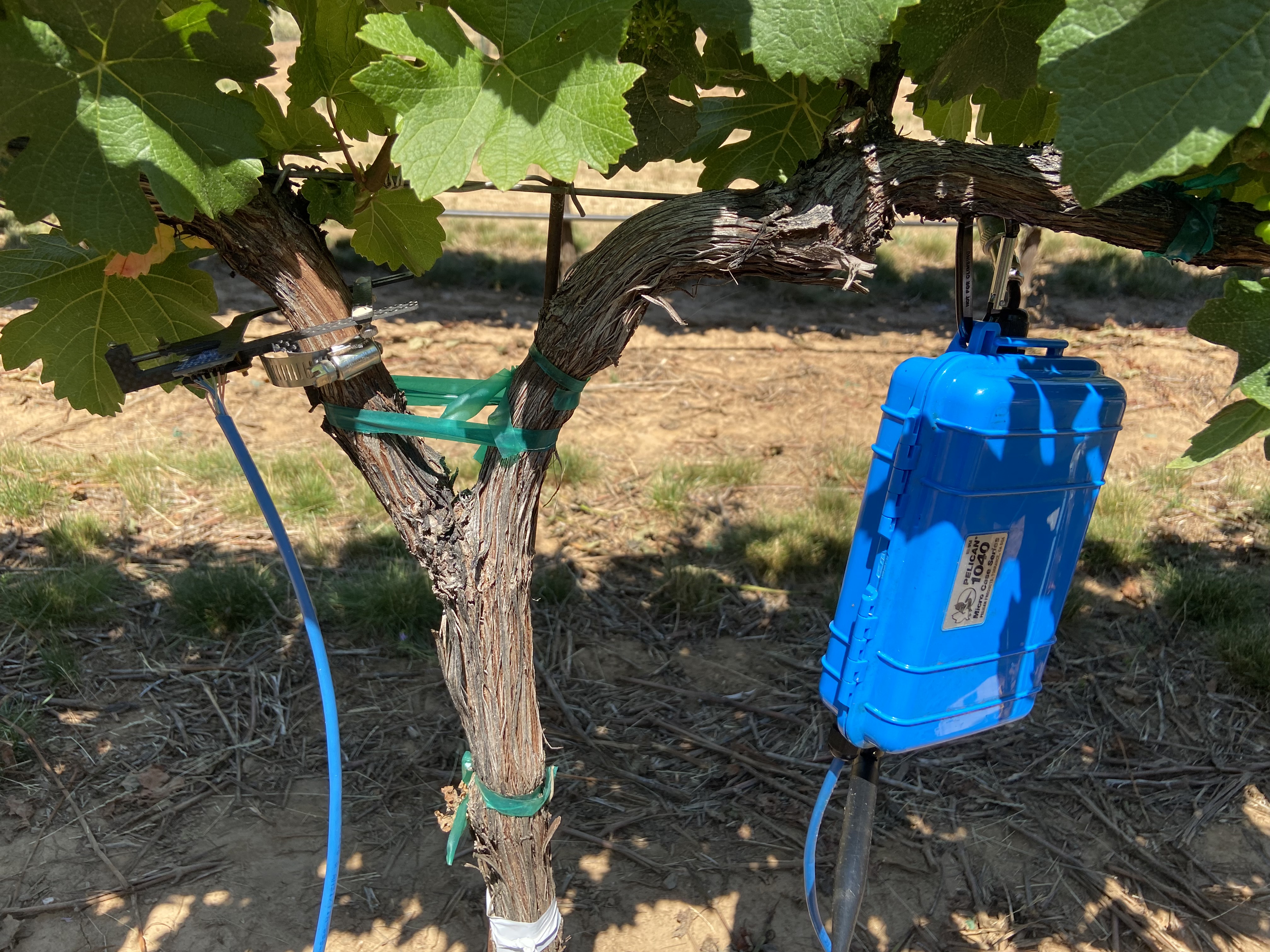
Figure 2: Dendrometer deployed on grapevine trunk at SOREC.
Show More
We got the results from the Lewis-Brown Farm deployment for some of the dendrometers as seen below. While most of the data was what we expected from our prototype, there were some graphs that had data that didn't seem accurate ranging from the displacement to temperature. For temperature, there were some outliers that we deduced was from direct sunlight over the sensor-- heating it up to a temperature not reflecting the environment. The inaccurate displacement data came from user errors such as magnet positioning during deployment to manufacturing errors. These errors are noted and will be marked down for future deployments and can be easily fixed. Also note that the displacement is graphed in mm instead of um. This was due to a programming error and will be fixed for the next deployment.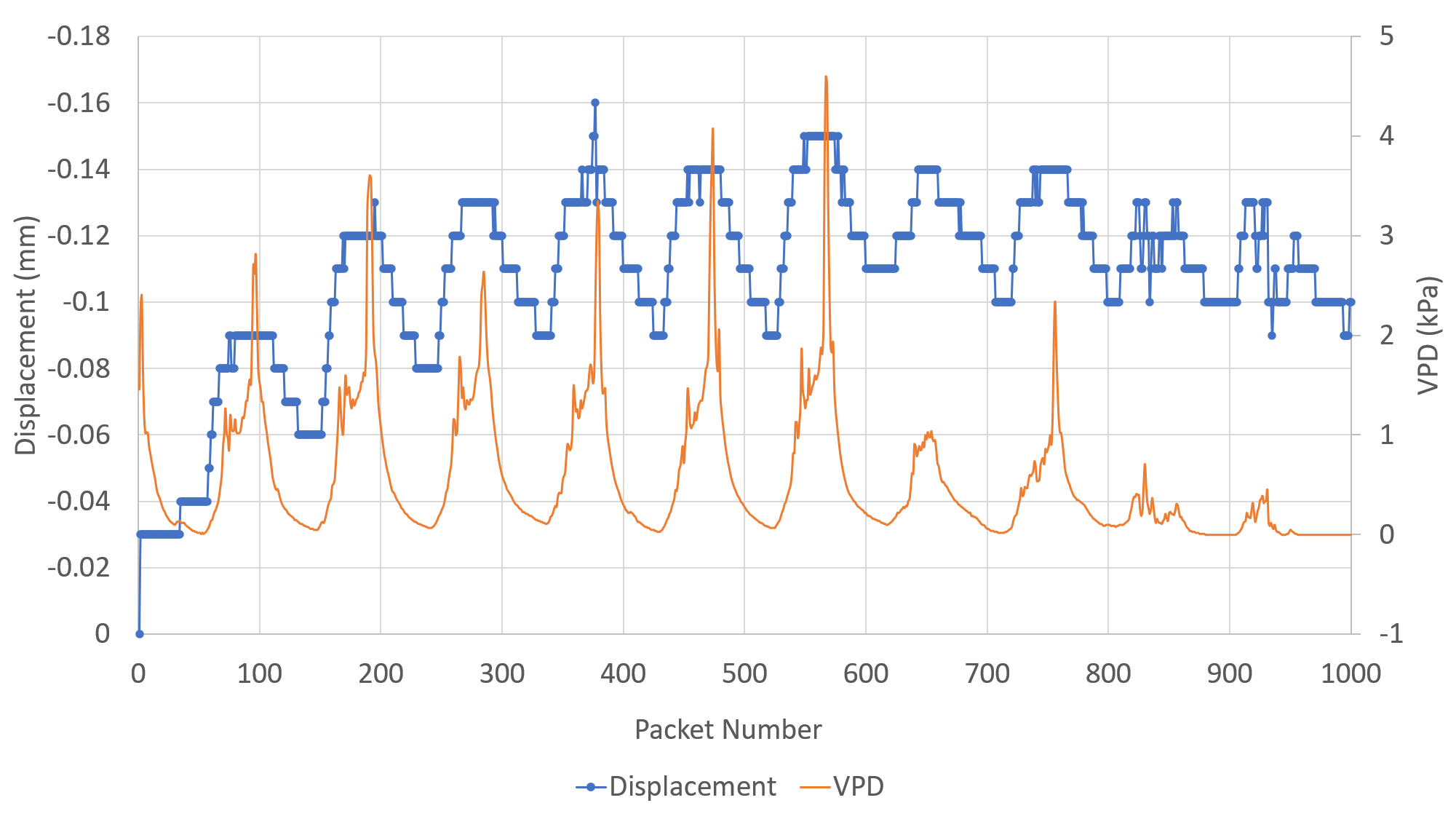
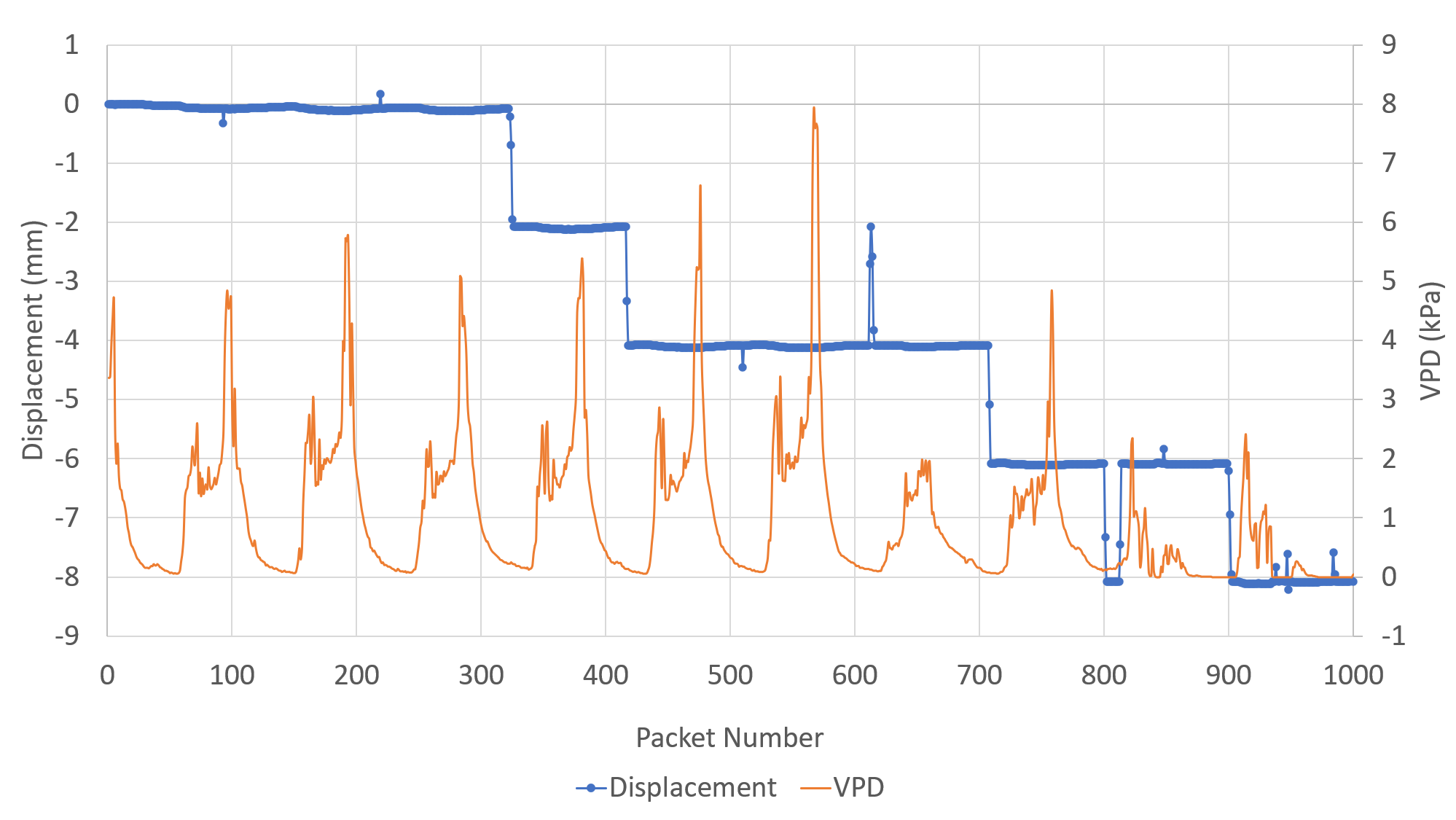
Show More
The latest version of the Dendrometer was deployed on a camellia plant for 3 days. Despite being winter time, the dendrometer was deployed to verify the prototype's functionality with the upgraded changes from the October deployment (including pelican box, PCB design, LED indicator, and error bug tracking).
Displacement and temperature logged for each measurement
Displacement and Vapor Pressure Deficit (VPD) showing that despite temperature changing, displacement changes with respect to VPD
Results:
- Consistent tracking of daily stem diameter between 15-33µm
- Error tracking reported 0 bugs during the 3 days
- Stem growth shows correlation with VPD as opposed to temperature, which is expected based on plant physiology and dynamics
Overall, the results were more successful than the last deployment; there were zero issues found in this trial, whereas the October trial showed some problems with code and overall design. This means that no measurements were excluded due to system functionality issues and all of the movements were tracked and recorded. The stem fluctuations were smaller compared to the last trial due to the time of year, as well as a different plant being tested. Through this trial, more features are being planned to increase the value of the prototype such as VPD calculations as well as LoRa communication.
Show More
Two dendrometers were deployed simultaneously at an OSU research facility for 10 days in October 2020. One dendrometer was placed on an 11-year old vine with Merlot grapes. The other was installed nearby on a Pyrex graduated cylinder (known to have no thermal expansion) to evaluate potential temperature dependency present in dendrometer data.
Displacement is recorded as a distance from initial position.
Results from Woodhall Vineyard Deployment:
- Consistently tracking daily stem diameter changes of approximately 150-200µm
- Device is mostly insensitive to temperature fluctuations
- Maximum 30µm recorded movement per day on Pyrex cylinder
Note: There are some initial jumps in displacement from the Dendrometer on Pyrex; the source of these jumps has not been identified. However, the measurements seem to stabilize after about 1.5 days. Additionally, gaps in the data exist from removed data values. At times, the Dendrometer recorded a serial position that did not reflect true position, which was evident because the data would jump to the beginning or end of the serial values (either 0 or 4095). To reduce noise in the graph, these values were removed.
We are currently working to incorporate LoRa (Long Range Communication) to enable dendrometer data to be transmitted up to 2-3 miles. This addition will allow farmers and researchers to obtain information regarding the growth of their vines without physically interacting with the system.
Improvements to the protection of the mechanical body and the AS5311 sensor will hopefully be included in the next iteration of the design. Additionally, we are working on a more streamlined production line.
Furthermore, mechanisms for further reducing any possible interference from weather are being developed to improve the overall robustness of the design and ensure a high level of data accuracy.
- HardwareX Paper
- Installation Guide
- Troubleshooting Guide
- Mechanical Assembly Guide
- Electronics Assembly Guide
- MongoDB Dashboard Guide
Vineyard, Woody Plants, Arduino, Carbon Fiber, Irrigation, Water-stress indicator, Maximum daily shrinkage, Trunk growth rate
[1] Conesa, M. R., Torres, R., Domingo, R., Navarro, H., Soto, F., & Pérez-Pastor, A. (2016). Maximum daily trunk shrinkage and stem water potential reference equations for irrigation scheduling in table grapes. Elsevier. Retrieved July 22, 2019.
[2] J.E. Fernandez and M.V. Cuevas, “Irrigation scheduling from stem diameter variations: A review,” Agricultural and Forest Meteorology, no.10, pp.136-149, Nov. 2009, doi: 10.1016/j.agrformet.2009.11.006.
- Project Planning
- Prototyping
- Synthesis
- Lab Testing
- Field Testing
- Finalization/Production
- Poster/Presentation
- Publication
- CRES
- Dendrometer
- Djinn
- eDNA Sampler
- eGreenhouse
- Evaporometer
- FloDar
- HyperRail
- Hypnos
- Isotopic Sampler
- Lilypad
- Loom
- Micro-Aggregating Sewer Sampler
- Mooraca
- OPEnSampler
- Pied Piper
- Rag Guard
- Rain Gauge Calibrator
- RainSavor
- RFID Moisture
- Sap Flow Meter
- SitkaNet
- Slide Sentinel
- Smart Rock
- Spool
- WeatherChimes
- Weed Warden
- Wisp
- Archived Project Blogs